Nov 6 2013
Standards and Opportunities for Deviation
“Every time you set a standard, you create possibilities for deviations, and the need to respond,” David Meier said. The setting was a presentation on problem-solving at a corporate in-house conference. It struck me as a concise statement of why managers should issue standards only where clearly and unquestionably useful.
Unnecessary standards were discussed in an earlier post, but the topic is worth revisiting in greater detail, first because there are so many of them in companies, making work life more complex than it has to be, and second, to elaborate on their impact on the organization.
Standards are rules set for others to follow, and rarely welcome, particularly when these others are thereby required to change behaviors they consider rational and appropriate, and sometimes more advanced than the standard. If you don’t enforce your unnecessary standard, your hurt the credibility of all your standards, including the useful ones; if you do, you turn into Captain Queeg, as he “tried to run the ship properly, by the book.”
The reception desk in the lobby of the building where the conference took place had a holder full of pens for visitors to sign in. No two pens were alike. A Captain Queeg would have had none of that; he would have mandated a model of pen and a color of ink, and set up regular audits to monitor compliance.
The example David gave was of office 5S zealots in Germany who had marked a location for a computer mouse on an individual’s desk and written him up for not complying. Last year, Mark Graban had posted a similar example of “5S” at a desk in the UK, shown on the right.
It reminded me of my experience of working in a Japanese office in the 1980s. It was a room with about 30 gray metal desks arranged in facing rows without any partitions. Everywhere else I have worked, each desk had its own supplies of staplers, staple-removers, scissors, glue sticks, etc., but it was not so in that office. These were shared resources, stored in a transparent plastic chest in the center of the room, with a label for each compartment.
This arrangement sounds right out of a Staples commercial, but that was the way it was. What struck me about it, however, was that the sharing created the need for labeled locations and for the discipline to return the items to assigned locations after use. This approach might make sense in offices used in hotelling mode. Everywhere else, however, each office worker has a dedicated desk that comes with a set of tools, that the employee organizes as he or she sees fit.
In the 21st century, the tidiness of desks does not have much to do with the performance of an office. What really makes a difference is the way information is organized on its computer network, and that is not visible when you walk through the office. But effective ways to do this are a whole other discussion. In factories, 5S in the offices is sometimes justified “to show solidarity with the shop floor.” It has been suggested to me that a better way to show solidarity might be to make the offices as hot, smelly and grimy as the shop floor.
Sometimes, the consulting companies that guide 5S implementation in client offices do not practice it in their own. In one particular firm, as consultants were in the field most of the time, they had no permanent desk, and grabbed an available one when they happened to be in town. With such a system, you might have expected the rooms to be numbered, and to have a magnetic board at the entrance with token for each present consultant to mark on a map of the facility where he or she could be found, but the managers felt that such a board would have been “ugly.” They never told me why they didn’t number the rooms. To locate a consultant you had to call his or her cell phone, and then follow instructions like “go left at the top of the stairs and it’s the third door to the right.”
Besides the size of steel balls at the end of motorcycle brake handles and company email addresses listed in my earlier post, there are many other things that are better off not standardized, and prominent ones include the analytical tools used in problem-solving.
The institutions of the quality profession in the US still promote as a standard the 80-year old tools of SPC, as if the art of collecting and analyzing data had not evolved since 1930. These tools are obsolete, but it would be a mistake to replace them with another set as a new standard.
There should be no standard. The professionals who work on improving quality should learn to use a broad variety of tools, and should be free to use whichever they think may help in their current circumstances. And they should always be on the lookout for new approaches and new technology.
Likewise, Value Stream Mapping (VSM) has, in the past 15 years, been elevated in the US to the position of a standard that all Lean practitioners are mandated to use. The need to map flows of materials and information in a manufacturing supply chain is often real, but there is no need for it to be done in a specific format with a specific set of symbols.
In fact, what happens in both situations is that formal compliance with the standard rapidly becomes the only criterion against which the outputs of quality or flow improvement teams are reviewed. The tools, their appropriate use, and their range of applicability are understood neither by the teams mandated to use them nor by the auditors who make sure they do, and the result is wallpaper.
Dec 6 2013
Confusion Over Standards: Limits or Basis for Innovation? | Industry Week Blogs | Jeffrey Liker
See on Scoop.it – lean manufacturing
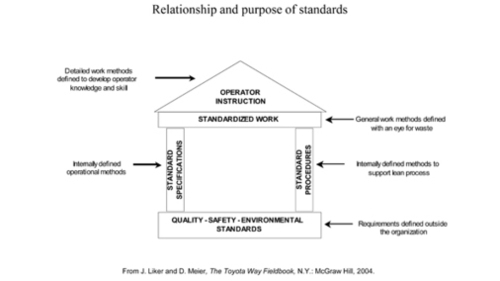
“As an undergraduate engineering student I spent a term in the offices of a nuclear power company writing standards. I sat at a desk, with a typewriter, and nuclear engineers fed me information while I wrote the standards. Standard 300.47.3.1. I had never been to a nuclear power site and had no idea what I was writing about, and I am pretty certain nobody at the site had memorized the tens of thousands of standards. They were aimed at the Nuclear Regulatory Commission who audited the company so we could prove we were safe. To the best of my knowledge pieces of paper never prevented a nuclear crisis.”
Jeffrey Liker chimes in on the issue of standards. While efforts to clear up the confusion on this topic in the context of Lean are praiseworthy, I think the terminology of “Standardized Work,” and “Work Standards” itself is hopeless.
Every author uses them differently, there is no hope of achieving consistency, and the word “standard” comes with too much undesirable cultural baggage, as illustrated by Jeffrey’s anecdote quoted above. As a result, every discussion of this topic is Tower-of-Babel project review.
Just because Toyota in the US uses terms doesn’t mean we have to, as they often are mistranslations of its own, Japanese terms, which themselves are not necessarily clear.
That’s why I prefer to talk about “work combos” for specifying how different tasks performed at different stations are combined into an operator job that fills the takt time, and “work instructions” for the breakdown of each task into steps with key points.
Then we can reserve the word “standard” for external mandates and internally generated rules and protocols used, for example, in quality problem-solving with suppliers.
See on www.industryweek.com
Share this:
Like this:
By Michel Baudin • Management 0 • Tags: Lean, Standard Work, Standards, Toyota