Nov 11 2011
Kanban On The Factory Floor
Via Scoop.it – The Kanban system
A software engineer discovers Kanban on the factory floor. http://t.co/FsBxAcbV…
Via blog.timwingfield.com
Nov 11 2011
Via Scoop.it – The Kanban system
A software engineer discovers Kanban on the factory floor. http://t.co/FsBxAcbV…
Via blog.timwingfield.com
By Michel Baudin • Blog clippings • 0 • Tags: Kanban, Lean, Lean manufacturing, Logistics, Toyota
Nov 11 2011
Professionals know that their productivity drops when they take on too many concurrent projects. An engineer whose attention is split across 15 projects doesn’t contribute effectively to any. But it happens because supervisors keep piling on assignments without regard to this phenomenon. Over the years, cures have been proposed under different names, all aiming to cap work in process.
About 1982, a colleague showed me the system he used to manage what he was working on. It was called the Scancard System, and it used the hardware in Figure 1. The cards were square, with 3 1/4-in sides and borders of different colors. They came with letter-size card pocket plastic boards that you could insert into 3-ring binders, keep on your desk or pin to a wall.
He used it with one column for his backlog of things to do, one column for work in process, and one column for completed items. It was a paper-based system but, at the time, so was almost everything we did. It gave you visibility, it capped the number of items you were working on at one time, and moving cards from one column to the next was an effective metaphor for the flow of your work. The ads showed smartly dressed managers using their scancard systems in meetings. I went for it and used it for years, until I had a project with a company that used another system and switched to fit in.
Fast forward to 2011. Scancard Systems is out of business, and I hear of a system called “Personal Kanban,” that is focused on providing visibility and limiting work in process, using a white board and Post-Its as in Figure 2:
I put quotes around the name because I find it to be little more than a feat of vocabulary engineering, leveraging the buzz around a feature of Toyota’s production control system to repackage ideas that have little to do with it, are very simple and have been around for a long time. A software developer visiting a factory may see a similarity with Toyota’s Kanbans, but it escapes me.
Of course, if, as in Figure 2, it is on a white board, you can’t carry it with you to a meeting or share it in your network. The Personal Kanban website advertizes an iPhone app called iKan, that I can’t find on Apple’s App Store. On the other hand, Leankit Kanban offers a web-based application with an iPhone version that looks very much like a team to-do list management system. It looks most useful if your work can be perceived as a collection of independent activities, which happens if each Post-It is for a whole project or for a prospect in a sales cycle. But it would not fit if each Post-It were for a task within a project, with precedence constraints or iterations between tasks.
Another limitation of such a status board is that is only shows current status, as compared, for example, with the Ybry chart of Figure 3, which shows the complete history of each project by using a line for each project rather than a card. Like the status board, it assumes that all project go through the same sequence of phases.
Figure 3. Ybry chart for projects going through the same sequence of phases
Ybry charts were invented by Charles Ybry in 1846 for railroad scheduling, and are still used for that purpose. See Edward Tufte’s Envisioning Information, pp. 107-110. The work-combination charts used in Lean operator job design are a variation on this method, as explained in Working with Machines, pp. 133-154.
By Michel Baudin • Management • 10 • Tags: industrial engineering, Lean, Management, Product development, Project management
Nov 10 2011
Using Opinel knives while picnicking last summer got me thinking about their differences in design philosophy from Swiss knives, our traditional perception of multifunction tools, and how smart phones and machining centers contradict that perception.
Mostly known for snow-capped mountains, the Savoie region of France is also the birthplace of the Opinel, a pocket knife designed 120 years ago, and very popular there with anybody who hikes or just goes on a picnic. As you can see below, it is a simple knife with a sharp, pointed blade, and a ring to lock it closed or open.
As a concept, it is diametrically opposed to its cousin, the swiss knife, and its multiple functions:
The Opinel only has one function, but performs it well; the swiss knife has many but does not excel at any. It will cut, but not as well as the Opinel; it serves as a corkscrew, but provides no leverage to pull out the cork; it will open cans, but slowly and by pulling the sharp edge of the lid outwards towards your hand rather than into the can, etc. It is convenient because you only have to carry one tool around, but, for everything it does, there is a dedicated tool that does it better.
When we think of dedicated versus multifunction tools, we usually think that they are like Opinels and swiss knives and that, when we add more functions to a tool, we necessarily compromise on performance or quality for each function. But is that necessarily true?
Our smartphones let us talk to each other but also contain the contact data of everyone we have met since elementary school. They tell you where we are on precise maps, wake us up in the morning, work as stopwatches and egg timers, play our music, receive our favorite radio station, identify a song from a snippet of a recording, etc.
Dedicated tools do not exist for everything a smartphone does and, when they do, rarely outperform the smartphone apps. For example, I have not seen an alarm clock do more than the clock app on my phone in terms of selecting whether it rings just once or every weekday at the same time, how loud, with what sound, etc.
What is it that makes a smartphone different from other multifunction devices? In what way is it not like a swiss knife?
The short answer is that a smartphone is a computer. We often think of computers as machines like any other, or worse when we are frustrated with confusing interfaces or system crashes, but the reality is that they are qualitatively different, and that programmability allows them to outperform dedicated tools. Their hardware configurations make them smartphones, game systems, laptops, or industrial controllers but, within this context, the range of services they can render well is limited only by the imagination and talent of programmers.
In production, machining centers or computer-controlled fabrication facilities are not swiss knives, in that their flexibility is not bought by a compromise in performance, and this has far-reaching consequences on production engineering and operations.
By Michel Baudin • Technology • 4 • Tags: Autonomation, Lean manufacturing, Manufacturing engineering, Technology
Nov 10 2011
Via Scoop.it – lean manufacturing
TOYOTA City, Japan — Even Steve Jobs, the management maverick and incurable tyrant knew that the best and time-tested strategy is none other than regularly securing the best possible ideas from workers than follow the dictates of a corporate…
Via www.bworldonline.com
By Michel Baudin • Press clippings • 0 • Tags: Lean, Toyota
Nov 9 2011
Managing Automation published another response to the same study that claims to show that Lean does not work: Lean Manufacturing and Operation Excellence: Not Worth Their Weight?
As described in the press and their own press release, the AlixPartners study commingles Lean with “Six Sigma and other productivity programs,” which raises the following issues:
If these press accounts are correct, the survey confuses Lean with other approaches in an open-ended list, misstates its purpose, and considers exclusively metrics of cost reduction.
The effectiveness of Lean is not an easy subject to study. Should we survey all the companies that claim to be Lean, have a Lean program in place, have been certified Lean by some external authority, or are top performers in their industry? Once we agree on this, we still need yardsticks to quantify both the effort they put into Lean and the rewards from it.
I took a stab at it a few years ago, and did my own analysis, the results of which were published as a Viewpoint in Manufacturing Engineering in 2006. I chose 40 winners of the Shingo Prize and searched Hoovers Online, for comparative performance data with their 400 top competitors. On the average, the data did not show that the Shingo Prize predicted any advantage in profitability, market share or employment growth. The AlixPartner press release says roughly the same thing, but I see it as reflecting on the Shingo Prize itself, not Lean.
The Shingo Prize is supposed to be the “Nobel Prize for Manufacturing,” but what are the criteria used to award it? You can download the Shingo Prize Guidelines and see for yourself. A team of Shingo Prize auditors visits the plants and awards points to measure “the degree to which the behaviors in an organization are aligned with the principles of operational excellence.” In other words, the plants are measured on process compliance. They score points for practices they have in place. It is like measuring chess players on the number of pawns they move, and is correlated to victory like the Shingo Prize to business performance.
Toyota did not grow based on a compliance checklist. When I visit a plant, based on what I see and what people tell me, I can form an opinion as to whether they are among the few that have the spirit of Lean or the many that are going through the motions. But I don’t know how to generate a checklist that could be systematically applied to arrive at such a conclusion, and, desirable though it may be, I don’t believe a real survey is feasible.
Jamie Flinchbaugh doesn’t like sports metaphors, but I can’t resist one here. Usain Bolt is the fastest man alive. Let us assume somebody publishes a book entitled “The Running Secrets of Usain Bolt.” How Usain Bolt actually trains is probably not trivial and certainly involves sustained effort and ferocious discipline. The author of the book, however, is concerned that a stern, eat-your-vegetables message would hurt sales, and focuses instead on easier topics, like shoes. As a result, kids flock to shoe stores thinking that wearing these shoes will make them fast, but the real ones are too expensive, so they buy cheap imitations instead. Six months later, based on their responses, a survey concludes that Usain Bolt’s methods don’t work.
Most Lean programs today are to serious implementations as cheap imitation shoes are to the training of Usain Bolt. Where they may succeed is in ruining the reputation of Lean. It is bound to happen sooner or later. As a brand, Lean has had a 22-year run so far, already longer than I expected.
By Michel Baudin • Management, Press clippings • 10 • Tags: Benchmarking, Lean manufacturing, Management, Strategy
Nov 11 2011
2011 Assembly Plant of the Year: Philips Doesn’t Rest on Lean Laurels – Cover Story – ASSEMBLY
Via Scoop.it – lean manufacturing
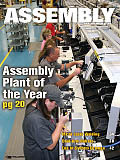
The article is from 9/26. and long in the tooth for a scoop, but the plant looks interesting.
Via www.assemblymag.com
Share this:
Like this:
By Michel Baudin • Press clippings • 0 • Tags: Lean assembly, Lean manufacturing, Line design, Manufacturing engineering