Nov 8 2011
Factory life with and without Kaizen
In Kaizen, Masaaki Imai describes Japanese executives returning in the 1970s to American plants they had visited thirty years before and being struck by the absence of change: they saw the same production lines with the same equipment operated the same way. This started me looking for photographic evidence. Overall, pickings were slim, but I did find the above pictures of the same coke oven at the Ford River Rouge plant shot in 1946 and 1976.
If there is Kaizen activity in a factory, how does it change the work life of employees at all levels? The following chart compares the breakdowns of their use of time, with and without Kaizen:
In a plant without Kaizen, operators and supervisors are fully occupied with routine daily tasks: production for the operators, expediting parts, enforcing discipline, and record keeping for supervisors. Only middle managers and executives spend a fraction of their time on projects involving capacity changes, new production lines or new technology. Nobody works on incremental improvements to the way the work is done today.
By contrast, Kaizen involves employees at all levels in such improvement activities to different degrees. Between improvement and daily routine, the boundary is sharp; between improvement and innovation, fuzzy. Over time, the cumulative effect of incremental improvement is radical change by itself. In addition, the skills acquired and the lessons learned from incremental improvements are incorporated into new line or plant design projects. In some Japanese auto parts plants, I remember seeing automatic lines side-by-side, where one used old machines that had been gradually retrofitted with devices that reduced the need for human intervention, while the other one had been built from scratch with new machines to be automatic. The Kaizen work done to implement the former was essential to the success of the latter.
Nov 8 2011
State prisons follow businesses by going ‘lean’
Whatever that might mean, Washington state prisons are “going Lean.” According to this article, it mostly means standardizing menus and meal times across the state.
Via Scoop.it – lean manufacturing
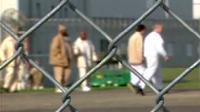
First state government went “green.” Now it’s gone “lean,” according to Department of Corrections staff.
Via www.king5.com
Share this:
Like this:
By Michel Baudin • Press clippings • 0 • Tags: Lean, Lean manufacturing