Feb 26 2013
New assembly methods at Toyota
Toyota’s latest plants in Ohira, in Japan’s Miyagi prefecture and in Tupelo, Mississippi, feature new approaches to assembly. According to press reports, the Miyagi plant is small, with 900 employees making 250 cars/day for export to the US, with a plan to double output and employment. It was designed to require a minimal investment and be easy to change. The plant started operations shortly before the Fukushima earthquake and, even though it is the Northern part of Japan that was most affected, it resisted well and was able to resume operations about six weeks later.
This is how Barry Render described it:
“The Miyagi factory is designed for advanced low-volume, hyperefficient production, with 1/2 the workers and 1/2 the square footage of Toyota’s 16 other plants. Inside, half-built Corollas and Yaris sit side-by-side, rather than bumper-to-bumper, shrinking the assembly line by 35% and requiring fewer steps by workers. Instead of car chassis dangling from overhead conveyor belts, they are perched on raised platforms. This is 50% cheaper, and also reduces cooling costs by 40% because of lower ceilings. Finally, the assembly line uses quiet friction rollers to move the cars along. The rollers use fewer moving parts than typical chain-pulled conveyor belts.”
Toyota is not providing details, but I have been able to glean some information about it from the press and Barry Render’s blog, on the following features:
- Side-by-side assembly
- Modular paint booths
- Friction roller conveyors
- Elevated platform versus suspension conveyor
This is followed by a few conclusions.
Contents
Side-by-side assembly

I have seen side-by-side assembly at the Volvo Bus factory in Turku, Finland. In the picture of the building below, bus bodies are assembled in the hall on the left, side-by-side under they are mounted on a chassis and move forward on their wheels, laid out front to back in the hall you see in the background.


The ratio of width to length is more favorable to this arrangement for buses than for cars. A straight assembly line with a front-to-back arrangement throughout would require a long and narrow building and a snaking line would have problematic turnarounds. With cars, the side-by-side arrangement seems suitable for work done at the front or the back of the car, such as installing headlights or bumpers. but less for work that requires access from the middle, such as installing instrument panels or upholstery. The following press picture (AP), however, shows an assembly operation done inside the car body in what appears to be a side-by-side layout. It implies that space for the part cart must be provided between cars, which forces them apart.

None of the available pictures from the Miyagi plant shows the raku-raku seat that was a prominent feature of the early 1990s designs and made it easier for operators to work inside the car bodies. Not only is a raku-raku seat an added investment, but it is also easier to use in a front-to-back than in a side-by-side layout.

Modular paint booths
I could not find pictures or sketches of the Miyagi painting system. Following is how CNN Money described it on 2/18/2011:
“…Toyota developed a modular paint spray line. The modules can be built somewhere else and are assembled at the plant in a much shorter time. Advantage: Cost savings. However, you don’t build a modular paint spray line factory somewhere unless you intend to build a lot of paint spray lines. Usually, cars get three coats of paint, usually water-based, and usually each coat is dried with heat. Not in Ohira. Here, the third coat is applied onto the still wet second coat and both are dried together. Advantage: Huge energy savings, faster paint time. Lower expenses…”
Friction roller conveyors
Following is how CNN Money described the Miyagi conveyor systems on 2/18/2011:
“Where the car moves along the floor, factories usually have below ground pits that house the motors, chains and gears that keep the line moving. Not in Ohira. Here, the cars move on maybe a foot high conveyor system that is simply bolted into the concrete flooring. Advantage: Cheaper to build, cheaper to tear down and rebuild somewhere else. The line can be lengthened or shortened at will. The assembly line doesn’t ‘grow roots’ as they say in Toyota-speak.”
Note that the sketch shows car bodies without wheels. In this system, the bar supporting the cars forms
A photographs of final assembly at Ohira shows operations done further downstream, with the wheels on:

In this picture, the floor the operators stand on is flush with the assembly line, meaning that it is either a classical line with the drive mechanism in a pit under the floor, or the operators are in a raised platform spanning the length of this assembly line segment.
Elevated platform versus suspension conveyor

The following photographs contrast the suspension conveyor approach as previously used at Toyota with the elevated platform at Tupelo, Mississippi:
From these pictures, it is clear that the elevated platform is a cheaper system to build, but I can see two issues with it:
- Flexibility in vehicle widths. The Yaris and the Corolla differ in width by less than half an inch, and therefore the same elevated platform can accommodate both. A Land Cruiser, on the other hand, is 11 inches wider, which makes you wonder whether it could share an elevated platform with the Yaris. The jaws of the suspension conveyor, on the other hand, look adjustable to a broad range of widths.
- Ergonomics. Working standing with your head cocked back and your arms overhead is just as ergonomically inadequate in both cases. By contrast, the VW plant in Dresden, Germany, uses suspended conveyors that can tilt the body, which is both ergonomically better and much more expensive:

Conclusions
The journalists take on the Ohira plant is that it is intended to prove a design for low-volume, low-cost, high-labor content plants that can be deployed easily in emerging economies with small markets. The designs of the early 1990s instead used more automation to make the work easier for an aging work force, with tools like the raku-raku seat. This is a different direction, addressing different needs. But why build it in Northern Japan rather than, say, the Philippines? It shows Toyota’s commitment to domestic manufacturing in Japan, and it is easier to test and refine the concept locally than overseas.
February 26, 2013 @ 5:25 pm
Thanks for the article. I never thought of turning the cars 90 degrees. We all need to “learn to see”.
February 27, 2013 @ 2:27 am
Thanks for the your continued sharing ! It is great to see the ‘side-by-side’ assembly concept. I believes most companies get into the ‘standardization & replicating’ the manufacturing system; which eventually leaves little room to explore other best means.
February 27, 2013 @ 6:25 am
Like the article you shared. And a quick question: do you think the side-by-side assembly would retain disadvantages of straight assembly, e.g. low flexibility?
February 27, 2013 @ 8:35 am
I wish I could give you an answer. This is the first time I hear of side-by-side assembly for cars, and increasing flexibility is not the reported motivation.
As I indicated, I have seen it in bus assembly. Buses are highly customized, but the customization is mostly in the upholstery and the outside paint, and takes place primarily at end of the process, where buses are laid out front-to-back.
February 27, 2013 @ 8:48 am
Comment in the Lean CEO discussion group on LinkedIn:
February 27, 2013 @ 9:52 am
Comment in the Lean Six Sigma Canada discussion group on LinkedIn:
February 27, 2013 @ 9:53 am
There is a US patent issued on 7/24/2007 to Yasushi Yamahara et al., from Toyota, entitled “Friction roller in conveyor.” The drawings appear to describe the system used at Ohira.
The illustrations about the Ohira plant also do not show a way to return the central bar from the end of the line back to the beginning. Another patent issued to Walter Schicht in 1985, is for an assembly line arrangement with friction rollers. The line is U-shaped, with carriers transferred sideways at the end (Fig. 3).
February 27, 2013 @ 9:23 pm
Comment in the Businessleanders.com discussion group on LinkedIn:
February 28, 2013 @ 4:42 pm
The side by side assembly was in place since the end of the 90’s for the assembly line of Mobilvetta motorhomes, and is in place right now for the first 5 stations of the new assembly line (end of 2009) of Elnagh, Mobilvetta and McLouis motorhomes in Poggibonsi (Italy).
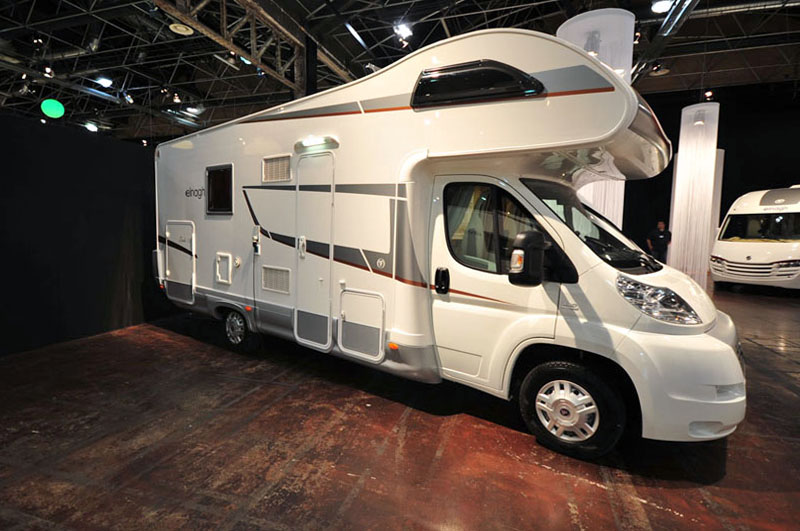
http://www.sea-camper.com
An Elnagh motorhome
February 28, 2013 @ 5:28 pm
Thanks. The width to length ratio of these products is similar to that of buses.
March 1, 2013 @ 7:31 pm
very intresting
March 3, 2013 @ 5:50 am
Very interesting to see the wheel being reinvented again. Many assembly methods and processes have be tried over the years by many companies and engineers. I have seen many myself but the key element here is to remember this is low volume production. I being a former former LSS champion of low volume production can speak to the advantages and disadvantages of it.
Most associates chose to work in low volume for several reasons… A few reasons are the ease of less repetitive work, less fatigue and better ergonomics conditions…less stressful (psychologically) work as opposed to high volume… Low volume typically has longer work cycles and more flexibility for creativeness. Low volume typically was where new product launches often take place before they get ramped up…There is often less cross training requirement than high volume where the need for cross training is much greater… Pride, integrity and ownership of associates have a higher requirement and demand for continuous improvements needs in low volume.
In other words you need to have very smart-sharp, focused and alert worker in these operations to make them work properly as they will be working more as teams rather than as individuals…If one team member cannot keep up the rest of the teams can be effected and a new member or a benchmarking procedure could be changed as with a process change request (PCR) or a new associate that can keep up…
I did experience this type of assembly operation many years ago at Ford Tractor operations where many teams and assembly methods and processes were used for low volume production but back then there was not a lot of automation or computerization yet.It was usually low volume,low demand. High volume high demand production methods and techniques used…Thanks and thank you Mr. Michel Baudin because I know from many of my past readings that you are one of the sharpest knifes in the drawer…Sincerely, Bill Ryan.
March 3, 2013 @ 9:35 am
Thanks for your kind words.
I do not understand why you say that low volume work needs less cross-training than high volume. I would have thought the opposite, with high volume supporting more specialization. If the volume is so low that you only need 1 person, that person clearly needs to know how to build the product from start to finish.
Best regards.
March 4, 2013 @ 12:29 pm
Comment in the Operational Excellence discussion group on LinkedIn:
March 4, 2013 @ 12:31 pm
Comment in the Operational Excellence discussion group on LinkedIn:
March 4, 2013 @ 12:34 pm
Comment in the Operational Excellence discussion group on LinkedIn:
March 4, 2013 @ 12:39 pm
Good point about accessing the open sides of two consecutive cars. I had missed that one.
I do not understand your points 4. to 6. Could you clarify?
March 4, 2013 @ 12:43 pm
Comment in the Operational Excellence discussion group on LinkedIn:
March 4, 2013 @ 12:49 pm
I have heard of this experiment, but I thought the location was Uddevalla rather than Kalmar. And, as I understand it, it was about not using assembly lines at all, which is quite different from what Toyota is doing in its new plants.
That fixed-station assembly is less productive than line assembly is a discovery that was made at Ford in 1913, and reverting to this old mode or operation sounds more like a rearguard action than pioneering work.
March 4, 2013 @ 12:53 pm
Comment in the Operational Excellence discussion group on LinkedIn:
March 4, 2013 @ 12:56 pm
Comment in the Operational Excellence discussion group on LinkedIn:
March 4, 2013 @ 1:03 pm
Comment in the Operational Excellence discussion group on LinkedIn:
March 4, 2013 @ 1:08 pm
Comment in the Lean Six Sigma Worldwide discussion group on LinkedIn:
March 6, 2013 @ 6:34 am
Comment in the Lean Six Sigma Worldwide discussion group on LinkedIn:
March 6, 2013 @ 6:37 am
Comment in the Lean Six Sigma Worldwide discussion group on LinkedIn:
March 6, 2013 @ 6:40 am
Comment in the Lean Six Sigma Worldwide discussion group on LinkedIn:
March 6, 2013 @ 6:41 am
Most manufacturers are committed to one way of making things. It has worked for them on some major products, so they consider it to be the “proven method” and apply it everywhere regardless of differences in product technology, mix, or demand pattern.
When they do try something new, they tend to do it in remote, foreign locations where the local management does not have the clout to resist the will of Production Engineering from the parent company.
What impresses me in the story of Toyota’s new plants is (1) their willingness to use a radically different design to meet different needs, and (2) their prudence is implementing it first in a domestic plant in Japan before deploying it elsewhere in the world.
May 28, 2013 @ 6:05 am
I hope that the disadvantages for this side by side concept would be solved in time.
July 14, 2017 @ 3:50 am
Is there any update to this story? Have you gotten more information about this factory?