Oct 31 2012
Takt time: can it be universally applied to all types of production?
This is the question Casey Ng asked in the TPS Only discussion group on LinkedIn. He elaborated as follow:
What are the essential conditions to implement takt time successfully? What are the cases when it fails and if you refer to the fundamental principle of takt and yet couldn’t find the solution? Then what are the exception areas and what alternate solution can be used?
To date, it has generated 43 comments, many with the high level of depth and the implementation examples that are characteristic to this group. It is a new LinkedIn group, with only 118 members — compared with 151,503 for Lean Six Sigma — but passionate and providing meaty technical content. I recommend it in general, and this discussion in particular. Here, I will be including only my own contributions on takt time, and its relevance to the following:
- Monuments
- Gigantic products with long takt times
- Refueling outages in nuclear power plants
- Rate work versus response work
- Non-repetitive operations
- Takt time and its calculation
- Takt-driven production as the ideal state
- Chronos, kairos, and takt time
Monuments
With monuments — the very large machines used for heat treatment, electroplating, painting, cutting of sheet metal, etc. — you usually have to load multiple parts simultaneously in order to meet demand, but these parts often do not have to be identical. I don’t recall anyone mentioning this in the earlier comments, but the parts that you load together can be a matching set rather than a batch. If your takt times are long enough, as, for example, in aircraft production, you can actually process one plane-set at a time, to takt time.
Gigantic products with long takt times
Gigantic products, like oil tankers, with takt times of six months or more, are built out of vertical hull slices made at much shorter takt times in a shop, and then welded together in the dry dock. Pioneered in the US with Liberty Ships during World War II, this is now standard shipyard practice, and enhances of the repetitiveness of the process, applying the concepts of takt time and one-piece flow.
Refueling outages in nuclear power plants
I am puzzled by Todd McCann‘s use of the takt time concept in the context of nuclear plant refueling outages, a problem I had the opportunity to work on 20 years ago in France, not in the US. I don’t know who the top performers are in this area today. At the time, it was a tie between the French and the Japanese, at about three weeks from shutdown to restart for one reactor, which is substantially longer than the 193 hours you were quoting for 2006, assuming that the work continues 24 hours/day, 7 days/week.
The French performance was accomplished by standardization. They had 55 reactors with only two designs, producing respectively 900MW and 1300MW, run by a single company. The procedures were the same everywhere, with any improvement quickly shared. The Japanese performance was based on using techniques from TPM. They had nine different reactor designs, run by different utility companies.
Even though they had the best performance in the world, I saw many opportunities for improvement, based on borrowing techniques from SMED, improved planning and scheduling for materials, tooling, and the 1000+ contractors involved, and operational details. Such a detail, for example, was security. Their procedures were effective at controlling access, but inefficient, with utility employees at all levels spending too much time getting contractors into and out of the facility.
The concept of takt, on the other hand, did not strike me as particularly relevant, given that a refueling outage is a yearly burst of intense activity for any given reactor, as opposed to a repetitive process.
Rate work versus response work
More generally about takt time, most businesses have both what my colleague Crispin Vincenti-Brown called Rate Work and Response Work. In manufacturing, if you do a Runner-Repeater-Stranger analysis of your products, Your Runners and Repeaters are rate work; your Strangers, response work.
Runners are products with enough volume to warrant a dedicated line. Repeaters are products that you group into families that, in aggregate, have enough volume for a line. Strangers are all the other products, including R&D prototypes, sample quantities of new products, spare parts for obsolete products, and any other special request. Even in aggregate, they account neither for a high volume nor for high revenue, but you still must produce them promptly. They require a small job-shop set up with your most flexible equipment, staffed with your most versatile operators, and its own operating policies.
While takt time is fundamental to line design for Runners and Repeaters, it isn’t much use for Strangers.
Non-repetitive operations
I have a hard time seeing the relevance of takt time in the absence of repetitiveness. In an assembly process, the takt time gives you an upper bound for the process time at each operation. As you broaden the mix of products you assemble on the same line, it becomes more difficult to balance the work among stations. Past a certain point, you are better off using approaches like bucket brigades, a.k.a. bump-back system, or even a yatai, which are not based on takt time.
Takt time and its calculation
Outside of mathematics, concepts are not reducible to formulas. Time/Demand is the way you calculate takt time, but it tells you neither the rules by which you are supposed to use that number nor how it maps to shop floor activity.
In mass production plants, managers use the inverse of this ratio: Demand/Time, which gives you the same information. Mathematically, working at a takt time of 1 minute and making 60 units/hour (uph) is equivalent. Yet, you and I know that, depending on whether the manager thinks the plant is producing at a takt time of 1 minute or making 60 uph, the shop floor will be radically different.
If you think in terms of uph, it doesn’t matter if nothing comes out for the first 59 minutes of each hour as long as all 60 come out in the end. If you think in terms of takt, 1 unit will come out like clockwork every minute.
What this says is that there is more to takt time than the formula. This is discussed extensively in Lean Assembly, with the following definition of takt time:
“Assuming we complete the product one unit at a time at a constant rate during the net available work time, the takt time is the amount of time that must elapse between two consecutive unit completions in order to meet the demand.”
As I recall, this is,more formally, the way Ohno described the concept in Toyota Production System.
Takt-driven production as the ideal state
The takt time allows you to define an ideal state, that John Shook and Pascal Dennis call True North, but that I prefer to call takt-driven production. In this state, you perform all operations one-piece at a time with process times that exactly match the takt time, and with instant transfer to the next operation at every beat. Of course, it is never perfectly realized, even on an assembly line. Real lines can only be approximations of it. The point is that it gives us a direction.
All deviations from takt-driven production translate to Ohno’s waste categories, overproduction, waiting, excess inventory, etc. Since any local project that move production in this direction eliminates waste, it can be undertaken with the confidence that it contributes to global improvement and is not sub-optimization.
Chronos, kairos, and takt time
Joachim Knuf : “… The ancient Greeks differentiated between two types of time: chronos (chronological, sequence of intervals, typically of equal extension) and kairos, best thought of as ‘the opportune moment.’ In this case, intervals begin and end under sets of conditions. This concept applies, for example, to healthcare, when next process steps are initiated by a preset configuration of values (patient’s blood pressure, glycemic index, bowel movement), not by elapsed time…”
I had never heard of Kairos, but, if the ancient Greeks made the distinction between Kronos and Kairos, why shouldn’t we? There is a rich toolbox associated with the pursuit of takt-driven production. Where the concept of takt does not apply, we can’t use these tools. As you said, extending usage of the word to Kairos-driven activities just adds confusion. These activities need different tools, and Casey pointed out some of them in his comments on Strangers. Let us keep different words to hang them on.
Jan 24 2013
Increasing Subassembly Productivity
See on Scoop.it – lean manufacturing
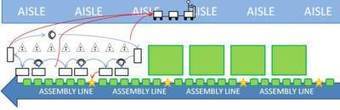
This is a rare post on assembly engineering, dealing with the layout of subasembly cells for a mixed-flow line. This is the red meat of Lean, ignored in most of the English-language literature on the subject. Kudos to Kelcy Monday for getting involved.
Reading this, I can’t help but thinking of many issues I would have handled differently, but I have not seen the product of the shop floor. In any case, this is the right opportunity to work on, with order-of-magnitude performance improvements at stake, as opposed to the 5% others might have nibbled by applying 5S on the old layout.
See on leanlogisticsblog.leancor.com
Share this:
Like this:
By Michel Baudin • Blog clippings • 0 • Tags: Cellular manufacturing, Lean assembly, Manufacturing engineering