Sep 27 2013
How Ford Eliminated Tickets on Flow Lines | Charles Sorensen | Bill Waddell
See on Scoop.it – lean manufacturing
“I am revisiting a great book – “My Forty Years With Ford” – written by Charles Sorensen. Sorensen was as close to being in charge of production at Ford during the Model T, genesis of the assembly line, $5 day era. The following is an excerpt […]
‘…a part such as a piston entered production bearing a ticket which covered every operation. If ten operations were involved, an entry was made on the ticket after each stage before proceeding to the next one. If one piston was lost in the move, all progress stopped until the missing piece could be found and accounted for. The time consumed in each operation was computed in lots of 100 or more, and results were tabulated on a card file which ultimately found its way back to the foreman so that he might check timing at each stage. Not only did the process mean delay from one operation to another, but when a motor assembler couldn’t get pistons, all car production was held up.’ “
It’s a great story. What Hawkins was implementing is now known as a traveller and, while not usually found in auto parts manufacturing, it lives on in other activities, where it is needed. I saw it in operation last week in small and mid-size plants in Germany that produce paints in thousands of shades in batches from 100Kg to 2,000Kg. Each batch has a traveller attached to it as a way to keep track of where it is in its process and which materials or pigments are needed for it.
In semiconductor manufacturing, you also have travellers, albeit electronic, to keep track of where a batch of wafers is in its 500+ operations process that involves multiple visits to the same equipment, and where the state of a wafer is not visually obvious.
The principle is not intrinsically wrong. The mistake Sorensen reports was applying it in the wrong place.
See on www.idatix.com
Oct 9 2013
Model T Assembly Line Starts For First Time – October 7, 1913 | The Truth About Cars
See on Scoop.it – lean manufacturing
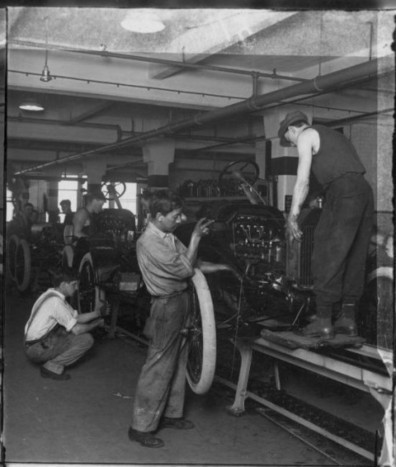
This is mostly interesting for the collection of photos from the Ford Highland park plant.
See on www.thetruthaboutcars.com
Share this:
Like this:
By Michel Baudin • Blog clippings • 0 • Tags: Assembly line, Ford