Jan 13 2012
5S First?
Via Scoop.it – lean manufacturing
I agree with the comments, but not with the heckler’s assumption that 5S is easy. It may look easy, but, if it really were, 5S efforts would be successful more often. The key reason it should almost never be done first is that it is so hard to make it stick. Companies that start with 5S usually have a big spring cleaning event followed by rapid backsliding that destroys the credibility of 5S with their work force.
A consultant who recommends 5S first is like a parent telling a kid to clean up his room because he has problems at school. It probably needs doing, but it won’t solve the school problems.
“Some time ago, while speaking at a conference in the land down under, I was taken to task by a participant for suggesting, “5S is usually the first improvement” in Lean implementation.”
Via oldleandude.com
Jun 12 2012
Just don’t start with 5S!
See on Scoop.it – lean manufacturing
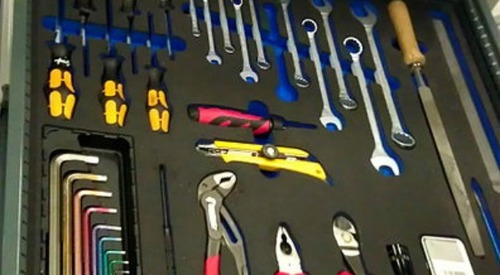
How many failed implementations will it take before consultants stop advising clients to start Lean implementation with 5S?
Telling people to start by tidying up their rooms works as well with manufacturing organizations as with teenagers. Try telling a machinist in a job-shop — who has spent the last 15 years making himself indispensable on a milling machine — that he should label hand-tool locations to make it easier for somebody else to do his job, and see how far you get.
5S is finishing work that you should undertake once you have changed the mode of operation. In cells, machinists in cells, who run multiple, different machines and rotate between positions need visible locations for tools, and will willingly maintain them.
Yet the following is what keeps getting posted on the web:
See on www.manufacturingdigital.com
Share this:
Like this:
By Michel Baudin • Management 6 • Tags: 5S, Lean, Lean implementation