Oct 13 2013
8 Reasons Lean Implementations Fail | Bill Waddell
See on Scoop.it – lean manufacturing
I came across this article titled “Top 5 Reasons Lean Projects Fail” and thought I would jot down my own list of 8 big reasons for lean failure: 1 Let’s start with his article – viewing lean as a collection of projects. Too…
Good insights! I will have to come up with my own list.
See on www.idatix.com
Oct 15 2013
Perfection Through Mistake-Proofing | IndustryWeek
See on Scoop.it – lean manufacturing
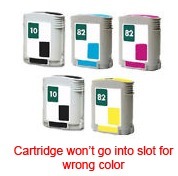
“Mistake proofing can make a significant difference in the output of any process [….] Mistake-proofing devices should meet three criteria:
The article makes the point that mistake-proofing must be “effortless.” The way I usually say it is that a mistake-proofing/poka-yoke device must not add labor, a point that is frequently missed in discussions of this topic in the US.
Why is it essential? Because any device that adds labor is guaranteed to be by-passed under pressure. If preventing a mistake requires one more gesture, on any day where “we have to ship all this by 6:00PM,” the organization will find a way around it.
Mistake-proofing makes a difference in any process where human error is a major cause of failure. Many processes qualify, but not all. If the main cause of defects is the machine’s inability to hold tolerances consistently, mistake-proofing will not do much good.
Yes, a device that is fallible cannot be considered mistake-proofing. Usability engineering, for example, provides user interfaces that make mistakes unlikely, but not impossible. Sometimes it is sufficient, but it is not mistake-proofing.
The one criterion I have an issue with is simplicity. A mistake-proofing device must be simple to use, I agree, and its design should not be anymore complex than necessary. However, where the stakes in human error are high, as in airliner cockpits or semiconductor process equipment, preventing mistakes may require elaborate technology. If a device for this purpose works every time and adds no labor, I see no reason to deny it the “mistake-proofing” label.
See on www.industryweek.com
Share this:
Like this:
By Michel Baudin • Press clippings, Technology • 2 • Tags: Mistake-Proofing, Poka-Yoke, Usability Engineering