Sep 6 2012
Journalist Confuses Activity and Growth
See on Scoop.it – lean manufacturing
In yet another examples of journalistic innumeracy, this article confuses a quantity, manufacturing activity, with its variation, growth.
The title “Manufacturing growth is down for third straight month,” leads you to believe it says that growth is lower but activity is still growing.
The first sentence confirms this: “Manufacturing growth in August remained as it had been in the previous two months—sluggish.” Sluggish does not mean negative.
But the next paragraph tells you that manufacturing activity had actually been contracting, not growing: “ISM’s index used to measure manufacturing activity, was 49.6 in August, which is 0.2 percentage points below July and 0.1 percent lower than June. A reading of 50 or higher indicates growth is occurring.”
See on www.logisticsmgmt.com
Sep 6 2012
Delhi Academic Bashes Indian Version of Lean – Forbes India
See on Scoop.it – lean manufacturing
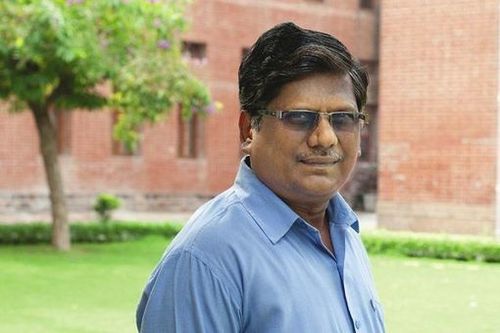
See on forbesindia.com
Share this:
Like this:
By Michel Baudin • Press clippings • 0 • Tags: Lean bashing