May 25 2012
Does management have a nationality? Interview with Konstantin Novikov
This is an interview conducted by Alexander Filippov in this month’s issue of Business Excellence, quoted in the Lean Forum, and translated by Michel Baudin. Konstantin Novikov is director of development at our Russian partner OrgProm. This article shows a Russian perspective on the challenges facing Russian business, and manufacturing in particular.
Konstantin Novikov: The laws of business management are international , but you can always find cultural differences in management styles. Do they make management stronger?
Alexander Filippov: Is there a Russian national character in management? Can you, in your opinion, subject Russia’s “generic features” to international standards?
KN: There are national features, of course. And if you wonder if they are good or bad, the answer is disappointing. Currently, they are bad.
The reason is a bad heredity. Let us remember the popular saying, and slightly rephrase it: “What is important in the life of a manager? Who his parents were, who he has learned from and whom he married … ” It is simple-minded folk wisdom but, in this case, it explains a lot. Who gave birth to modern Russian management? Repressive post-Soviet management, dense as a Pithecanthropus. What examples did we learn from? The dramatic post-Soviet experience of the remnants of state industrial enterprises, yes, but more often – from our own mistakes. And it has not been the most effective teacher: it is sick and cannot teach the faithful how to search for a brighter future.
And we “married” mergers and acquisitions (often hostile), ignoring worthy “brides” like effectiveness and productivity.
If you try to identify “generic features” of Russian management, the first thing we should mention is the fear of problems and the unwillingness to solve them, based on lack of ability. In this sense, it is appropriate to recall the key words of managers from different cultures. The American says: “The problems – they are a challenge for me;” the Japanese, “Problem solving – it’s a daily routine. Problems are good. It is bad when there are no problems.” A Russian manager is likely to say: “The problems are headaches.” You see the difference?
As for the reduction of specific features of Russian management at a certain standard, it must be understood that there are different international standards for management. Who said that the international way is always good! That’s why I do not understand why we should be brought down to somebody else’s idea? This is the way to eternal backwardness. What we need is the most advanced management, and we won’t settle for anything less.
And yet we don’t need to brood. Now Russian management has no problem in learning scientific management. There just was no serious need to do so . But things change very quickly …
AF: Much is said about the laziness and conservatism of our managers …
KN: The laziness and conservatism of Russian management are only the symptoms of the problem, not the problem itself. And life happens in different ways. There are leaders who “plow” for 16 hours a day. Only a few benefit from it, the efficiency is low. Intensifying managerial work does not give results. It causes heart attacks and strokes, but the early death of leaders is not economically advantageous for the country. It is more important to get to the root causes of key problems. Not all managers of industrial enterprises realize that they no longer have time to lose. For many the crisis is already personal — the executive armchairs are “burning” under them. The market will not wait. Russian state component factories, for example, has long lost theirs orders to foreign component manufacturers even for customers like state-owned Oboronprom.
Still, many executives, managers, and, I think, even workers in general, believe that Lean and effective management are a fad that will pass, and that the state will not abandon its defense industry. Such leaders are carriers of an unacceptable management style and will soon leave the stage.
The problem is not in the machines, equipment and new lines. It is the system that created and reproduces the people who are at the controls of enterprise management. The problem is antiquated, obtuse forms and methods of management. The system, which had previously coped with the task of managing people in the production process, and can no longer cope. In its depths are useless and operate manufacturing processes. If the processes are bad, the results are unsatisfactory.
AF: Does the situation change with the formal accession of Russia to the WTO?
KN: The formal accession is just formal. It is unlikely to affect the quality of business management. Management decisions depend on the competence of managers themselves. And we still have low competence. Resulting in an inability to work as a team, and in the absence of leadership as a phenomenon. And the list goes on.
AF: Is a continuing recession or a protracted crisis necessary to push management to improve
KN: Crises are good “levers of change”, but it is not always the case. Much depends on company CEOs. Only the top person can initiate the changes to the system. The people below can only destroy the system. These are the laws of the existence of systems.
AF: There are already many expatriates in Russian management. Will Russia turn into a settling tank for underachieving foreign consultants?
If you look deeply, it becomes clear that this will not happen. If a manager or consultant is of no use, how long will the business owners who will keep him around?
AF: Are we seeing the Does the germs of a qualitatively new, competitive management?
KN: Yes. And it is sure to come! As conditions change, new people emerge – with new knowledge and skills. Previously, people with this temperament were less in demand. I am personally acquainted with the new industrial leaders. And a characteristic of this new leadership that is key to effectiveness is that people do things without being ordered to or even asked.
The leaders of this “new wave” – are still no more than 5% of the managers. But they are the catalysts of growth and will “reset” the economy.
Jul 10 2012
Photos of SSJ 100 Nose and Rear Production – English Russia
See on Scoop.it – lean manufacturing
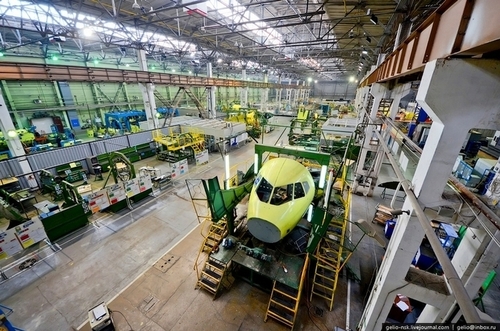
The Chkalov factory makes nose and rear sections for the Superjet 100, Sukhoi’s entry in the regional jet market, in competition with Embraer and Bombardier. While praised for its design, the Superjet 100 has been late in ramping up production and its future is in jeopardy following a crash during a demonstration in Indonesia on May 9, 2012.
According to the article, the plant has a Lean program in place. Based on the photographs, the manufacturing concept is fixed-station assembly with kitting.
See on englishrussia.com
Share this:
Like this:
By Michel Baudin • Press clippings 0 • Tags: Aeronautics, Lean manufacturing, Russia