Mar 13 2012
How to eliminate “Muri,” or overburdening
“Muri, Muda, Mura” is often mentioned in the Japanese manufacturing literature as a trio of evils to avoid. Of the three, Muda gets the most attention. Usually translated as waste, it designates everything we do in a factory that is unnecessary. For a change, let us focus on Muri.
Muri, in everyday Japanese, means impossible, with the nuance of unreasonable or unsustainable. A person working exceptionally hard is said to be doing Muri. Other words are used to say that something would violate the laws of physics, or that it is socially improper or inopportune. When there is Muri in your process, it means that you are asking people to work too hard, which results in defects, burnout, repetitive stress injuries, or even accidents. Conversely, removing Muri means making your process humanly sustainable, so that is can be executed as well at the end of a shift as at the beginning, by a 50-year-old or a 20-year-old, a man or a woman, 5 or 7 feet tall.
It cannot be repeated often enough that Lean is not about making people work harder but instead, in the tradition of Frank and Lillian Gilbreth, in making the work easier to do. When you observe a truly Lean plant, you do not see operators hurrying. Instead, you see them working steadily, at a sustainable pace, at jobs that are carefully choreographed for effectiveness and efficiency. A key example of Muri elimination is the raku-raku seat shown above. It is a device introduced at Toyota in the 1990s and now adopted by many car makers to remove the need for operators to crawl into car bodies in order perform assembly tasks inside.
There are many tools to remove Muri. You can easily notice that an operator is overburdened by direct observation in the shop. A more systematic approach is to use Toyota’s TVAL to rate jobs based on the weight operators have to carry and how long they have to carry it. TVAL establishes an equivalence between combinations, so that, for example, carrying 4 lbs for 200 seconds is equivalent in terms of fatigue impact to carrying 10 lbs for 4 seconds. You then focus on the jobs with highest TVAL ratings and improve these jobs to reduce it.
Once you know which job to focus on, you record it on video and review it with the operator to identify ways to make it easier or to offload parts of it to others with lighter burdens. If the job involves interactions between operators and machines, you analyze with with a work combination chart to improve task sequencing and identify tasks within the job that need better tooling or a better work station layout.
Mar 27 2012
General Electric CEO Jeffrey Immelt: 600 to run new line at Louisville’s Appliance Park
Via Scoop.it – lean manufacturing
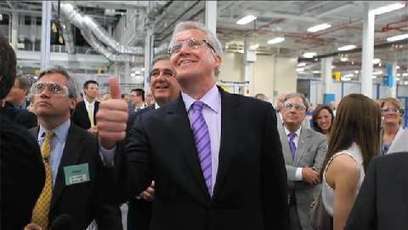
The plant is described as a “Toyota-style, lean, manufacturing line.” Current GE CEO Jeffrey Immelt does not once mention his predecessor’s flagship initiative, Six Sigma.
Via www.courier-journal.com
Share this:
Like this:
By Michel Baudin • Management 0 • Tags: Lean, Lean manufacturing, Toyota