“Recently I revisited Avanzar, Toyota’s interior and seating supplier for their San Antonio, Texas truck plant. Most major suppliers are on-site delivering directly to the factory which in the case of seat assembly is right across a wall. Avanzar’s CEO, Heriberto (Berto) Guerra, was very excited about their Japanese advisor, formerly of Toyota, and all he had been teaching them about real kanban. I had visited a year earlier and Mr. Guerra was very excited about their Japanese advisor, formerly of Toyota, who was teaching them kanban. A year before that, he said they were making progress in a few model areas and now there was kanban everywhere. Mr. Guerra also raved about the way their advisor was teaching them 5S, which again I found confusing.”
Michel Baudin‘s insight:
A well-documented case of Lean implementation at a just-in-sequence supplier ot seats to Toyota’s plant in San Antonio, TX. An oddity of this case is that they lump under the “5S” label all sorts of changes that are well beyond it, such as redesigning part presentation at assembly to make frequently used items easily accessible, or kitting parts.
Of course, as long as it works for them, they can call it whatever they want. For communication with the rest of us, however, as Jeffrey found, it is confusing.
Apr 9 2013
Flow improvements called “5S” at Avanzar | Jeffrey Liker
See on Scoop.it – lean manufacturing
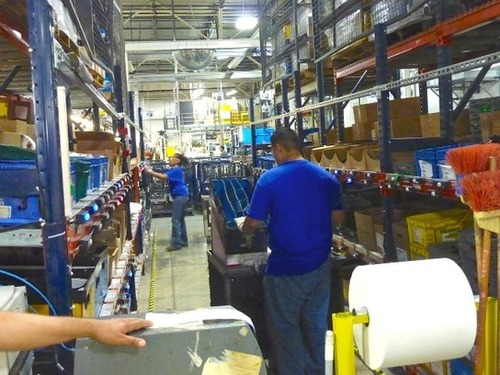
“Recently I revisited Avanzar, Toyota’s interior and seating supplier for their San Antonio, Texas truck plant. Most major suppliers are on-site delivering directly to the factory which in the case of seat assembly is right across a wall. Avanzar’s CEO, Heriberto (Berto) Guerra, was very excited about their Japanese advisor, formerly of Toyota, and all he had been teaching them about real kanban. I had visited a year earlier and Mr. Guerra was very excited about their Japanese advisor, formerly of Toyota, who was teaching them kanban. A year before that, he said they were making progress in a few model areas and now there was kanban everywhere. Mr. Guerra also raved about the way their advisor was teaching them 5S, which again I found confusing.”
A well-documented case of Lean implementation at a just-in-sequence supplier ot seats to Toyota’s plant in San Antonio, TX. An oddity of this case is that they lump under the “5S” label all sorts of changes that are well beyond it, such as redesigning part presentation at assembly to make frequently used items easily accessible, or kitting parts.
Of course, as long as it works for them, they can call it whatever they want. For communication with the rest of us, however, as Jeffrey found, it is confusing.
See on www.manufacturingpulse.com
Share this:
Like this:
By Michel Baudin • Press clippings • 2 • Tags: 5S, 94306, Just-in-sequence, Kanban, Lean, Lean manufacturing