Dec 21 2014
History of technology
Mar 5 2012
Masaaki Imai Remembers Taiichi Ohno
Via Scoop.it – lean manufacturing
This article includes interesting details about Ohno’s background and early life, from someone who has actually met him.
Via www.gembapantarei.com
Share this:
- Click to print (Opens in new window) Print
- Click to share on Facebook (Opens in new window) Facebook
- Click to share on LinkedIn (Opens in new window) LinkedIn
- Click to share on Reddit (Opens in new window) Reddit
- Click to share on X (Opens in new window) X
- Click to email a link to a friend (Opens in new window) Email
By Michel Baudin • Blog clippings • 0 • Tags: History of technology, Lean manufacturing, Toyota, TPS
Mar 2 2012
The origins of Lean – as viewed in France’s L’usine Nouvelle
The French magazine L’Usine Nouvelle is similar to Industry Week in the US and has a special place in my heart as the first organization ever to pay me for my writings. I wrote an article for them on quality in Japan in February,1981, and they sent me a check.
Last week, the current editor in chief, Thibaut de Jaegher, wrote the editorial translated below:
At the origins of lean manufacturing
Published February 25th, 2012 at 11 55 | L’Usine Nouvelle No. 3273
Everyone seeks their own production system. The Renault-Nissan Alliance has its production way, and so does Michelin. Alstom has developed its Apsys, SEB its Operational Performance Plan …
Since the publication of the book “The Machine That Changed the World” in 1990, manufacturers worldwide have embarked on a frantic quest to eliminate waste, improve quality, and increase productivity.
Because this book coined the phrase lean manufacturing, we also think that Toyota is the instigator of these organizational methods. It is not the case.
Since industry has been industry, manufacturing engineers have sought to continuously improve their manufacturing methods. It only became a Japanese specialty after World War II. Before, the search for more efficient production systems and a scientific organization of labor was rather the prerogative of the Americans.
The first production standards have emerged during the Civil War, to facilitate the repair of guns on the battlefield. The American system of manufacturing (ASM) was used to accelerate the manufacture of guns and their maintenance during operations.As in the Toyota production system, this organization was based on two pillars: standardization and mechanization. And one might think that all sites of Springfield (the manufacturer of rifles) turned in just in time because of the war.
The ASM was probably one of the competitive advantages that allowed the “Yankees” to win.
This is another article that denies the contributions of the developers of Toyota’s system. To say that they did not invent anything and that everything they have done is just a rehash of American industrial engineering is like saying that Einstein’s theories are that a copy of Newton, Maxwell, Lorenz, etc..
As in all disciplines, advances in production techniques are based on previous achievements. The American System of Manufacture is a set of techniques aimed at the manufacture of interchangeable parts. It dates from the 19th century. It included among other things, technical drawings, the concepts of critical dimensions and tolerances, and it got the machine tools industry started. This a major contribution, somewhat forgotten because industry around the world has so thoroughly assimilated it.
And the Toyota system is built on this foundation, incorporating further elements from Taylor, Gilbreth, the engineers at Ford or GM, not to mention TWI. That does not mean that people at Toyota have added nothing there, or that their ability to incorporate these elements into a coherent and efficient whole is negligible. The Machine That Changed The World is a good book, which introduced the term “Lean”, but we should not overestimate the importance. By other names, the approach had already aroused a sustained interest in industry for at least 10 years it came out. My own introduction to the topic dates back to 1980.
Thibaut de Jaegher in turn responded as follows;
@ Michel Baudin
My paper does not deny the contribution of Toyota in the history of production but just reminds readers that there were production systems well before the TPS. Which you also recognize claiming that Toyota was inspired by American methods, and particularly what I wrote about, to invent its own model.
And an anonymous other reader chimed in as follows:
@ Reglede3
This is very true. Americans, for the purposes of the conflict, however, have pushed the system of standardization to its logical conclusion.In fact, it was the French who invented standardization (in the late 18th century) in the manufacture of guns (a lock adapting to any gun or butt). It passed to the United States through sales of French guns to the “insurgents”. The English invented the standardization of nuts and bolts.
I have several issues with this exchange. The first is the attribution of inventions to nations. As such “the French,” “the Americans,” “the English,” or “the Japanese” don’t invent anything; inventors are individuals, and sometimes teams. It’s not, “the Americans” who invented the assembly line but a team working at Ford in the 1910s, including Charles Sorensen, P.E. Martin, Clarence Avery, and others. Attributing nationalities to inventions is neither fair to inventors nor useful, because all it does is make the inventions more difficult to adopt outside their countries of origin.
The second point is that both the editor in chief and the anonymous reader are surprisingly casual about historical accuracy, considering that “the French” are known for historians like Fernand Braudel, who make cautious inferences from thorough research. Just-in-Time production of rifles in the Civil War? Interchangeable parts in the Revolutionary War? Come on! As often, the Wikipedia article on the American System of Manufacturing, and its list of references, is a good place to start checking the facts.
Why should we care? Because interchangeable parts technology is the first example of a successful, decades-long government-funded R&D program in the United States, and refutes the widely-held belief that all innovation comes from the private sector. It was the first in a line of such efforts that, in recent decades, includes the Apollo program and the Internet.
Does it have anything to do with Lean? Yes, but so indirectly as to be irrelevant. The creators of TPS, like Taiichi Ohno, acknowledge Ford’s mass production system, as an inspiration both on what to do and what to change, and Ford’s system could not have existed without interchangeable parts.
Share this:
- Click to print (Opens in new window) Print
- Click to share on Facebook (Opens in new window) Facebook
- Click to share on LinkedIn (Opens in new window) LinkedIn
- Click to share on Reddit (Opens in new window) Reddit
- Click to share on X (Opens in new window) X
- Click to email a link to a friend (Opens in new window) Email
By Michel Baudin • Press clippings • 2 • Tags: History of technology, Lean, Lean manufacturing
Nov 21 2011
An Alternative to Kanban: One-Piece Continuous Flow
Via Scoop.it – lean manufacturing
This is a guest post by Jim Coplien on Jeff Sutherland’s blog. Jim’s research seems thorough
Via scrum.jeffsutherland.com
Share this:
- Click to print (Opens in new window) Print
- Click to share on Facebook (Opens in new window) Facebook
- Click to share on LinkedIn (Opens in new window) LinkedIn
- Click to share on Reddit (Opens in new window) Reddit
- Click to share on X (Opens in new window) X
- Click to email a link to a friend (Opens in new window) Email
By Michel Baudin • Blog clippings • 0 • Tags: History of technology, Lean
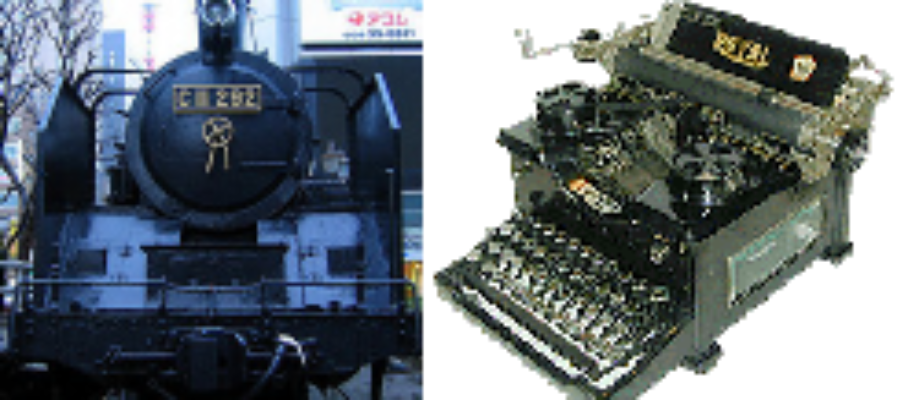
Oct 25 2011
The steam locomotive and the typewriter
The first draft of my book Working with Machines contained a chapter that was a post-mortem on two obsolete machines, which was cut on the grounds that, unlike all other chapters, it was not actionable for the reader.
Its abstract is as follows:
The steam locomotive and the typewriter are icons of the industrial age, and their parallel histories show different aspects of the human experience of working with machines. The steam locomotive is fondly remembered; the typewriter, all but forgotten except for the QWERTY keyboard. The steam engine participated in the development of every industrial economy, but the typewriter played no major role in Japan. The typewriter did not demonstrably improve the productivity or quality of office output, but was adopted only because of its image of modernity.
Locomotive driver was a prestigious position for a manual laborer, but typist never was. Compared to electrics and diesels, the steam locomotive had a cab that was exposed to the elements and to the heat of the firebox and therefore uncomfortable, difficult to operate, and dangerous. Yet engineers and firemen preferred it to the tedium and loneliness of modern locomotives. Automatic machines that require human attention only when they malfunction are also in airplanes and in manufacturing plants, challenging the job designer to keep the operator alert and used efficiently.
As the typewriter prints one keystroke at a time, typists were always busy with a single machine and determined both its productivity and output quality. Typists worked in comfortable places, but under pressure, and faced the long-term hazards of sedentary work. The typewriter’s main legacy is that a society can make a long-term investment in machines whose tangible benefits do not obviously exceed their costs.
Click here for a pdf file of the entire chapter.
Share this:
- Click to print (Opens in new window) Print
- Click to share on Facebook (Opens in new window) Facebook
- Click to share on LinkedIn (Opens in new window) LinkedIn
- Click to share on Reddit (Opens in new window) Reddit
- Click to share on X (Opens in new window) X
- Click to email a link to a friend (Opens in new window) Email
By Michel Baudin • History • 1 • Tags: History of technology, industrial engineering, Lean manufacturing, Manufacturing engineering
Mar 12 2017
Meeting with Christoph Roser in Paris
Christoph Roser, who blogs at AllAboutLean.com, is another on-line correspondent whom I had a chance to meet on this trip. We discussed our backgrounds and shared interests over a brasserie lunch in Paris, across from the Luxembourg gardens, where we walked afterward, among Parisians enjoying the early spring, playing tennis, and watching puppet shows. At one edge of the gardens is the seat of the French Senate; at the opposite, my alma mater, Mines-Paristech.
As authors, Christoph and I have been working with the same publisher, Taylor & Francis, and even with the same editor. His “Faster, Better, Cheaper” in the History of Manufacturing came out last year, covering the period “from the stone age to Lean Manufacturing and beyond,” which is very ambitious. I confessed to not having read it cover to cover, but the parts I did read seemed carefully researched. Unfortunately, the way things are made hasn’t been as thoroughly documented as wars and revolutions, and it’s a challenge to trace back the origins of ideas in this area that we apply every day.
Share this:
Like this:
By Michel Baudin • News • 1 • Tags: Christoph Roser, History of technology