Mar 17 2014
Averages in Manufacturing Data
The first question we usually ask about lead times, inventory levels, critical dimensions, defective rates, or any other quantity that varies, is what it is “on the average.” The second question is how much it varies, but we only ask it if we get a satisfactory answer to the first one, and we rarely do.
Mar 18 2014
A Definition of Lean | Mike Rother
See on Scoop.it – lean manufacturing
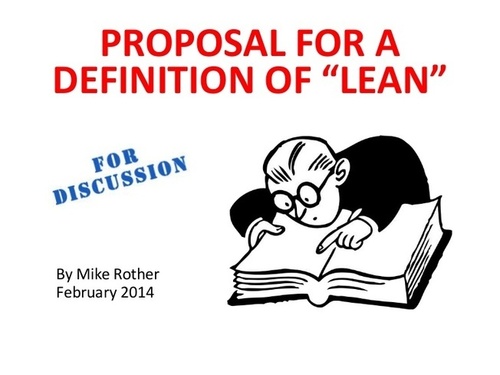
The proposal is “Lean is the permanent struggle to flow value to one customer.”
Permanent struggle is fine, but I prefer pursuit. It means the same thing but it is shorter and “pursuit of happiness” sounds better than “permanent struggle for happiness.”
On the other hand, I have a problem with “flow value,” which I see as the sort of vague abstraction that would prompt Mike Harrison to ask whether it come in bottles. It is exactly what Dan Heath is warning against in the video included in the slideshare.
I also have a problem with the exclusive focus on customers, which I see as Business 101 rather than Lean. Lean includes many features like heijunka, that are intended to make life easier for suppliers and are transparent to customers. Going Lean means looking after all the stakeholders of the business, not just its customers.
This is why I define it instead as the pursuit of concurrent improvement in all dimensions of manufacturing performance through projects that affect both the production shop floor and support activities.
Yes, I know, it is specific to manufacturing, but that is not my problem.
See on www.slideshare.net
Share this:
Like this:
By Michel Baudin • Blog clippings • 4 • Tags: Lean, Mike Rother