May 9 2012
Goodyear Tire & Rubber Co: Fayetteville – Business Excellence Magazine
See on Scoop.it – lean manufacturing
A case study, presented by the plant manager.
See on www.bus-ex.com
May 9 2012
See on Scoop.it – lean manufacturing
A case study, presented by the plant manager.
See on www.bus-ex.com
By Michel Baudin • Press clippings 0 • Tags: Lean, Lean manufacturing, Management, TPM
May 3 2012
See on Scoop.it – Cellular manufacturing
When companies implement lean manufacturing correctly they achieve necessary cost improvements and increase productivity while maintaining operational control that only on-shore, in-sourced production offers.
See on d2pnews.com
By Michel Baudin • Blog clippings 0 • Tags: Lean, Lean manufacturing, Management, Strategy
May 3 2012
See on Scoop.it – lean manufacturing
A great article by Lonnie Wilson, pen-pal of over 10 years.
Focus on lean and get those cost reductions, and more.
See on www.industryweek.com
By Michel Baudin • Press clippings 0 • Tags: Cellular manufacturing, Lean manufacturing, Metrics
May 2 2012
See on Scoop.it – lean manufacturing
I don’t agree with everything this blogger says, particularly when he describes the establishment of the Roman empire as a “short term” fix. In my book, 400 years of peace and prosperity is beyond the short term…
On the other hand, I think he is right when he says that “Kaizen events” are not performing continuous improvement. As an oxymoron, “Kaizen Blitz” is even better: it mixes Japanese and German in a concoction that literally means “lightning strike of continuous improvement.”
The so-called “Kaizen event” is a good tool when applied to the right opportunities, but there are two problems with it:
The French did even worse by calling the same method “Hoshin Events,” literally meaning “compass needle event.” The equally unfortunate consequence is that it makes it impossible to discuss Hoshin Planning with them.
See on www.impomag.com
By Michel Baudin • Blog clippings 2 • Tags: Continuous improvement, Kaizen, Management
May 9 2012
It’s Time to Rethink Continuous Improvement – blogs.hbr.org (blog)
See on Scoop.it – lean manufacturing
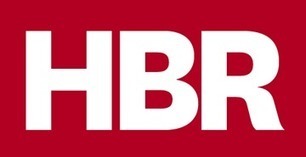
Who else is shocked by a phrase like “Six Sigma, Kaizen, Lean, and other variations on continuous improvement…”?
Since when is Lean a variation on continuous improvement? Instead, continuous improvement is a component of Lean, which includes many features that are not continuous improvement.
Kaizen does not belong in a list in parallel with Lean. It literally means “improvement” and is used in Japan to mean continuous improvement. In other words, this entry in the list refers to the list itself.
Six Sigma is a method developed at Motorola in the US to solve process capability issues and is not continuous improvement.
Is it one more list patterned after Borges’s classification of animals?
See on blogs.hbr.org
Share this:
Like this:
By Michel Baudin • Blog clippings 2 • Tags: Continuous improvement, Kaizen, Lean, Six Sigma