Jun 30 2012
Is there a “DIY” AGV in your future? – DC Velocity
See on Scoop.it – lean manufacturing
This is what jidoka/autonomation is about! Contrary to what you read in the reductionist literature, jidoka is not just about stopping machines when they start to malfunction. It is instead a complete and intelligent approach to automation.
See on www.dcvelocity.com
Jul 3 2012
A Video Showing Office 5S Gone Wrong
See on Scoop.it – lean manufacturing
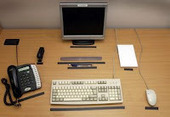
Not fresh news, but my colleague Maria Samsonova just pointed it out to me.
See on www.leanblog.org
Share this:
Like this:
By Michel Baudin • Blog clippings 2 • Tags: 5S, Office Lean